WD-40. The name itself conjures images of squeaky hinges, stubborn bolts, and that distinct, recognizable scent. It’s a staple in garages, workshops, and homes across the globe, touted as a miracle solution for countless problems. But when it comes to electronics, the question of whether WD-40 is a suitable electrical contact cleaner arises, and the answer is more nuanced than a simple yes or no.
Understanding Electrical Contact Cleaners and Their Purpose
Before delving into WD-40’s suitability, it’s crucial to grasp the function of electrical contact cleaners. These specialized products are designed to remove dirt, dust, grease, oxidation, and other contaminants from electrical contacts, connectors, and circuit boards. These contaminants can impede electrical flow, leading to poor performance, intermittent connections, and even complete equipment failure.
Electrical contact cleaners achieve this by dissolving or dislodging these contaminants, leaving behind a clean, residue-free surface that promotes optimal electrical conductivity. The key is a residue-free finish; any remaining substance can attract more dirt and further hinder performance over time. They’re also formulated to be safe for use on various materials commonly found in electronics, such as plastics, metals, and rubber.
What Exactly is WD-40? Its Composition and Properties
WD-40 is a complex blend of various components, primarily designed as a water displacement and rust preventative. Its exact formula is a closely guarded trade secret, but its key ingredients are known to include mineral spirits, petroleum distillates, aliphatic hydrocarbons, and carbon dioxide propellant.
Its primary functions are to loosen rusted parts, displace moisture, penetrate and lubricate, and protect against corrosion. The mineral spirits and petroleum distillates act as solvents, dissolving grease and grime. WD-40’s water displacement properties stem from its ability to form a thin, protective barrier that prevents moisture from contacting the metal surface.
However, WD-40 is not solely a lubricant; its lubricating properties are considered relatively light and short-lived compared to dedicated lubricants. Over time, the lighter solvents evaporate, leaving behind a heavier, oily residue. This is where the controversy regarding its use as an electrical contact cleaner stems from.
The Argument Against Using WD-40 as an Electrical Contact Cleaner
The central argument against using WD-40 on electrical contacts revolves around its residue. While it effectively dissolves contaminants initially, the oily residue it leaves behind can attract dust and dirt, forming a sticky film that actually worsens the problem in the long run.
This residue can also potentially interfere with sensitive electronic components, altering their electrical characteristics and leading to malfunctions. In some cases, the residue can even contribute to corrosion, especially in humid environments.
Furthermore, WD-40 is not specifically designed to be safe for all types of plastics and rubber commonly found in electronics. While it may not immediately cause damage, prolonged exposure can lead to degradation, cracking, or swelling of these materials, compromising the integrity of the device.
The propellant used in WD-40, while necessary for dispensing the product, can also be problematic. Some propellants are flammable, posing a fire hazard if used near sparks or open flames. While WD-40 itself is not highly flammable, the presence of flammable propellants warrants caution.
When Might WD-40 Be “Acceptable” (But Still Not Ideal)?
In extremely limited circumstances, WD-40 might be used as a temporary solution if a proper electrical contact cleaner is unavailable. This applies only to less sensitive components and in situations where immediate action is necessary to restore functionality.
For example, if a heavily corroded connector is preventing a vital piece of equipment from operating and no dedicated cleaner is on hand, a small amount of WD-40 might be used to loosen the corrosion. However, it’s crucial to thoroughly clean the area with a lint-free cloth afterwards to remove as much of the residue as possible.
Even in these situations, it’s important to understand that using WD-40 is a compromise and carries the risk of long-term problems. It’s always preferable to use a dedicated electrical contact cleaner designed for the specific task.
Choosing the Right Electrical Contact Cleaner: What to Look For
Selecting the appropriate electrical contact cleaner is essential for ensuring effective cleaning and preventing damage to electronic components. Key considerations include:
- Residue-Free Formula: Opt for a cleaner that evaporates completely, leaving no residue behind. This is the most critical factor.
- Material Compatibility: Ensure the cleaner is safe for use on the various materials present in the device, including plastics, metals, and rubber. Check the product label for specific compatibility information.
- Non-Conductive: The cleaner should be non-conductive to prevent short circuits and electrical damage.
- Fast-Drying: A fast-drying formula minimizes downtime and reduces the risk of moisture-related problems.
- Safety Precautions: Pay attention to safety warnings and follow the manufacturer’s instructions carefully. Use in a well-ventilated area and avoid contact with skin and eyes.
There are different types of electrical contact cleaners, including:
- Solvent-Based Cleaners: These are effective at dissolving grease, oil, and other contaminants.
- Water-Based Cleaners: These are generally safer for the environment and less likely to damage sensitive components.
- Foam Cleaners: These are ideal for cleaning hard-to-reach areas and vertical surfaces.
Safe Application Practices for Electrical Contact Cleaners
Even with the right cleaner, proper application is crucial for achieving optimal results and preventing damage. Here are some essential tips:
- Disconnect Power: Always disconnect the power supply before cleaning any electrical components. This is a fundamental safety precaution.
- Ventilation: Work in a well-ventilated area to avoid inhaling harmful fumes.
- Protective Gear: Wear gloves and eye protection to prevent skin and eye irritation.
- Application Method: Apply the cleaner directly to the affected area, using a spray nozzle or a lint-free cloth. Avoid oversaturation.
- Cleaning Action: Gently scrub the area with a brush or swab to remove stubborn contaminants.
- Drying Time: Allow the cleaner to dry completely before reconnecting the power supply.
- Testing: After cleaning, test the device to ensure it is functioning properly.
Alternatives to WD-40 for Common Problems
While WD-40 might seem like a universal solution, there are often better alternatives for specific problems.
- For Lubrication: Use a dedicated lubricant, such as silicone spray or lithium grease, for long-lasting lubrication of moving parts.
- For Rust Prevention: Apply a rust preventative coating, such as a corrosion inhibitor, to protect metal surfaces from rust.
- For Cleaning: Use a specialized cleaner designed for the specific type of surface or material.
- For Water Displacement (Electronics): Use a dedicated electronic cleaner formulated for safe and effective water displacement.
Conclusion: WD-40 – Proceed with Caution (or Avoid Altogether)
In conclusion, while WD-40 possesses some cleaning and water displacement properties, it’s generally not recommended as a primary electrical contact cleaner due to its residue. The potential for long-term problems and damage outweighs any short-term benefits. A dedicated electrical contact cleaner is always the safer and more effective choice. By understanding the properties of WD-40 and the specific requirements of electrical contact cleaning, you can make informed decisions and ensure the longevity and performance of your electronic devices. Opting for specialized products and following proper application practices will minimize risks and maximize the effectiveness of your cleaning efforts. Remember, prevention is always better than cure, so regular cleaning with the correct product can prevent issues arising in the first place.
What is WD-40, and what is it typically used for?
WD-40 is a widely recognized and versatile product primarily used as a water displacement agent, lubricant, and rust preventative. Its formulation consists of a blend of petroleum-based solvents, mineral oil, and other ingredients that contribute to its multi-purpose capabilities. Common applications include loosening rusted bolts, preventing corrosion on metal surfaces, and displacing moisture from mechanical parts to improve their functionality.
While WD-40 is excellent for these tasks, it’s crucial to remember its intended purpose. It’s not specifically designed as a cleaner, and especially not as an electrical contact cleaner. Its oily residue can attract dust and debris, potentially hindering long-term electrical performance. Therefore, using it in unintended applications requires careful consideration and awareness of potential drawbacks.
Why is it important to use a designated electrical contact cleaner?
Designated electrical contact cleaners are specifically formulated to dissolve contaminants like oxidation, grease, and grime without leaving behind residue. This is crucial because residue can impede electrical conductivity, leading to malfunctions, signal degradation, and even equipment failure. These cleaners are typically non-conductive and fast-drying, ensuring optimal contact performance after application.
Using the correct cleaner safeguards sensitive electronic components and minimizes the risk of damage. These specialized cleaners maintain the integrity of electrical connections, promoting reliable performance and preventing costly repairs. They are engineered to not only clean but also to protect against future corrosion, extending the lifespan of electrical equipment.
Can WD-40 clean electrical contacts at all?
WD-40 can temporarily remove some surface-level dirt and grime from electrical contacts. Its solvent properties may help dissolve minor contaminants, and the pressurized application can dislodge loose particles. However, this cleaning action is superficial and doesn’t address the underlying issues of oxidation or long-term protection.
The primary concern is that WD-40 leaves behind an oily residue. This residue, while initially seeming helpful by preventing rust, can attract dust and debris, ultimately degrading contact performance over time. Therefore, while it might offer a short-term solution in a pinch, it’s not a substitute for a proper electrical contact cleaner.
What are the potential risks of using WD-40 on electrical contacts?
The main risk associated with using WD-40 on electrical contacts is the creation of a conductive residue layer. This oily film can trap dust and dirt, forming a paste that actually interferes with electrical conductivity, leading to intermittent connections or complete failure. This is particularly problematic in sensitive electronic devices.
Furthermore, WD-40’s oily residue can also damage certain plastics and rubber components commonly found in electrical connectors and housings. This can lead to cracking, swelling, or degradation of these materials, further compromising the integrity of the electrical system. The long-term consequences can be more costly than simply using a proper cleaner.
Are there specific types of electrical contacts where using WD-40 is particularly dangerous?
Using WD-40 is particularly dangerous on sensitive electronic components, such as those found in circuit boards, sensors, and precision instruments. The fine pitch of these components means that even a small amount of residue can significantly disrupt their operation. Any residual oil can cause short circuits or inaccurate readings, leading to equipment malfunction.
Similarly, contacts that carry low-voltage signals, like those in audio equipment or data communication systems, are highly susceptible to interference from WD-40’s residue. The film can act as a dielectric, weakening the signal strength and causing distortion or data loss. These systems require clean, unobstructed connections for optimal performance.
If I accidentally used WD-40 on electrical contacts, what should I do?
If you’ve accidentally used WD-40 on electrical contacts, the first step is to thoroughly remove as much of the product as possible. Use a clean, lint-free cloth to wipe away the excess. Avoid spreading the residue further; instead, gently blot the area to absorb the oil.
Next, clean the contacts with a designated electrical contact cleaner. Apply the cleaner according to the manufacturer’s instructions, ensuring it reaches all affected areas. Allow the cleaner to dry completely before restoring power to the equipment. This process will help dissolve and remove the WD-40 residue, restoring proper contact conductivity.
What are some safe and effective alternatives to WD-40 for cleaning electrical contacts?
The most effective alternatives to WD-40 for cleaning electrical contacts are specifically formulated electrical contact cleaners. These products, available at most electronics and hardware stores, are designed to dissolve contaminants without leaving behind residue. Look for cleaners that are labeled as “non-conductive” and “fast-drying” for optimal results.
Another effective option is isopropyl alcohol (IPA) with a concentration of 90% or higher. IPA evaporates quickly and leaves minimal residue, making it a suitable cleaner for many electrical components. However, it’s crucial to ensure the IPA is completely dry before powering on the equipment. Always follow safety precautions when using solvents and work in a well-ventilated area.
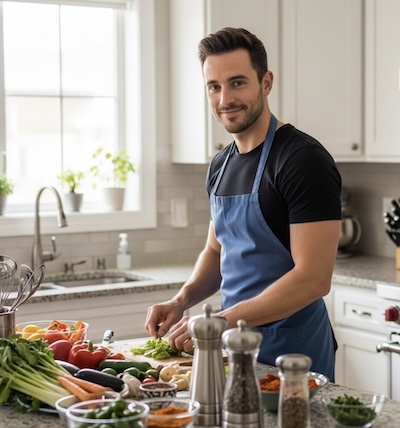
Alden Pierce is a passionate home cook and the creator of Cooking Again. He loves sharing easy recipes, practical cooking tips, and honest kitchen gear reviews to help others enjoy cooking with confidence and creativity. When he’s not in the kitchen, Alden enjoys exploring new cuisines and finding inspiration in everyday meals.