Creating a vacuum chamber might sound like a project reserved for high-tech laboratories, but with the right knowledge and readily available materials, you can construct a functional and simple vacuum chamber at home. This guide will walk you through the process, from understanding the basics of vacuum technology to assembling your own setup.
Understanding the Fundamentals of Vacuum Technology
Before diving into the construction process, it’s crucial to grasp the core concepts behind vacuum technology. A vacuum, in essence, is a space devoid of matter. Achieving a perfect vacuum is impossible, but we can create environments with significantly reduced pressure compared to atmospheric pressure.
Vacuum Levels: Different applications require different vacuum levels. We typically categorize vacuum levels as rough, medium, high, and ultra-high. The chamber described in this guide is intended for rough to medium vacuum applications.
Pressure Measurement: Pressure is measured in various units, including Pascals (Pa), Torr, and millibars (mbar). Atmospheric pressure at sea level is approximately 101,325 Pa, 760 Torr, or 1013 mbar. A rough vacuum is typically considered to be in the range of 100 to 1000 Pa.
Vacuum Pumps: Vacuum pumps are the heart of any vacuum system. They remove gas molecules from the chamber, reducing the pressure inside. Different types of pumps exist, including rotary vane pumps, diaphragm pumps, and diffusion pumps. For a simple vacuum chamber, a rotary vane pump is often the most practical and affordable choice.
Choosing the Right Materials and Components
Selecting the appropriate materials is paramount to ensure your vacuum chamber is both effective and safe. A poorly constructed chamber can leak, making it impossible to achieve the desired vacuum level.
Chamber Body: The chamber body is the main container that will hold the vacuum. A sturdy metal pot, a thick acrylic box, or even a repurposed pressure cooker can serve as the chamber body. Metal is often preferred due to its strength and ability to withstand pressure differences. However, acrylic allows for visual monitoring of processes inside the chamber.
Sealing Materials: A reliable seal is essential to prevent leaks. O-rings made of materials like Viton or Buna-N are commonly used. These materials are flexible and create a tight seal when compressed. Ensure the O-ring is compatible with the materials being used inside the chamber.
Vacuum Pump: A rotary vane pump is a common choice for achieving a rough to medium vacuum. Consider the pump’s pumping speed, measured in liters per minute (LPM) or cubic feet per minute (CFM). A higher pumping speed will evacuate the chamber faster.
Vacuum Gauge: A vacuum gauge is necessary to monitor the pressure inside the chamber. Analog gauges are simple and affordable, while digital gauges offer more precise readings.
Fittings and Tubing: Use vacuum-rated fittings and tubing to connect the pump to the chamber. These fittings are designed to withstand vacuum pressures and prevent leaks. Choose materials compatible with the pump and chamber.
Vacuum Grease: Apply vacuum grease to O-rings and fittings to ensure a proper seal. Vacuum grease is specifically formulated to have low outgassing properties, meaning it won’t release contaminants into the vacuum environment.
Building Your Simple Vacuum Chamber: Step-by-Step Instructions
Now that you have a basic understanding of the principles and materials, let’s move on to the construction phase. This guide will focus on building a vacuum chamber using a metal pot as the main body.
Preparing the Chamber Body
The first step is to prepare the metal pot. Ensure it’s clean and free of any rust or debris. If the pot has a lid, check that it fits snugly. If not, you may need to modify it or replace it with a custom-made lid.
Drill a hole in the lid to accommodate a vacuum fitting. The size of the hole will depend on the fitting you choose. Ensure the hole is precisely drilled to prevent leaks.
Smooth the edges of the hole to prevent damage to the O-ring. Deburring the hole with a file or sandpaper is essential.
Installing the Vacuum Fittings
Install the vacuum fitting into the hole you drilled in the lid. Use an O-ring between the fitting and the lid to create a vacuum-tight seal. Tighten the fitting securely, but avoid over-tightening, which could damage the O-ring.
Add any additional fittings needed for gauges, valves, or feedthroughs. The specific fittings will depend on your intended use for the vacuum chamber.
Connecting the Vacuum Pump
Connect the vacuum pump to the fitting on the chamber lid using vacuum-rated tubing. Ensure the tubing is securely attached to both the pump and the fitting. Use hose clamps to provide additional security.
Check the pump oil level before operation. Many rotary vane pumps require oil for lubrication and sealing.
Sealing the Chamber
Apply a thin layer of vacuum grease to the O-ring on the pot. This will help to create a better seal between the pot and the lid.
Carefully place the lid on the pot, ensuring the O-ring is properly seated. Apply even pressure to the lid to create a tight seal. You may need to use clamps or weights to hold the lid in place.
Testing the Chamber
Turn on the vacuum pump and monitor the pressure gauge. The pressure should gradually decrease as the pump removes air from the chamber.
Check for leaks using a leak detector or by applying soapy water to the seams and fittings. If you see bubbles forming, it indicates a leak. Tighten the fittings or reapply vacuum grease to the O-rings to address the leak.
Continue to monitor the pressure gauge to ensure the chamber is holding a vacuum. The achievable vacuum level will depend on the quality of the chamber construction and the pump’s performance.
Troubleshooting Common Issues
Building a vacuum chamber can sometimes present challenges. Here are some common issues and how to address them.
Leaks: Leaks are the most common problem encountered when building a vacuum chamber. Check all fittings, O-rings, and seams for potential leaks. Use a leak detector or soapy water to pinpoint the source of the leak. Tighten fittings, replace damaged O-rings, or reapply vacuum grease as needed.
Insufficient Vacuum: If you’re not achieving the desired vacuum level, several factors could be responsible. Ensure the vacuum pump is functioning correctly. Check the pump oil level and replace the oil if necessary. Verify that all connections are tight and leak-free. The chamber materials themselves can also be a source of outgassing, which limits the achievable vacuum.
Pump Overheating: Vacuum pumps can overheat if they are run for extended periods or if they are working too hard. Ensure the pump has adequate ventilation. Check the pump oil level and replace the oil if necessary. If the pump continues to overheat, it may be necessary to use a larger pump or to reduce the workload.
Safety Precautions
Working with vacuum systems can be dangerous if proper safety precautions are not followed.
Implosion Hazard: Vacuum chambers can implode if they are not strong enough to withstand the pressure difference between the inside and the outside. Use caution when working with vacuum chambers, and always wear safety glasses. Never exceed the chamber’s pressure rating.
Pump Oil: Vacuum pump oil can be harmful if ingested or inhaled. Use caution when handling pump oil, and always wear gloves. Dispose of used pump oil properly.
Electrical Safety: Vacuum pumps are powered by electricity. Ensure the pump is properly grounded and that all electrical connections are secure. Never operate the pump in wet or damp conditions.
Applications of a Simple Vacuum Chamber
A simple vacuum chamber can be used for a wide range of applications, including:
Vacuum Degassing: Removing dissolved gases from liquids, such as resins or silicones.
Vacuum Sealing: Creating airtight packages for food or other products.
Educational Demonstrations: Illustrating the effects of vacuum on various materials and processes.
Small-Scale Experiments: Conducting experiments that require a controlled vacuum environment.
Enhancements and Modifications
Once you have a basic vacuum chamber, you can enhance its functionality with various modifications.
Adding a Viewport: Installing a viewport allows you to observe the processes occurring inside the chamber without breaking the vacuum.
Installing Feedthroughs: Feedthroughs allow you to introduce electrical signals, fluids, or gases into the chamber without compromising the vacuum.
Integrating a Temperature Control System: A temperature control system can be used to heat or cool the chamber, allowing you to conduct experiments at specific temperatures.
Cost Considerations
The cost of building a simple vacuum chamber can vary depending on the materials and components you choose. A basic setup using a repurposed metal pot and a small rotary vane pump can cost as little as $200 to $500. More sophisticated setups with larger chambers, more powerful pumps, and additional features can cost several thousand dollars.
You can save money by using repurposed materials and by sourcing components from online retailers or surplus stores. However, it’s important to prioritize quality and safety when selecting materials and components.
Conclusion
Building your own simple vacuum chamber is a rewarding project that allows you to explore the fascinating world of vacuum technology. By following the steps outlined in this guide and taking the necessary safety precautions, you can create a functional and useful tool for a wide range of applications. Remember to prioritize safety, choose quality materials, and thoroughly test your chamber to ensure it is operating correctly. With a little patience and effort, you can create a vacuum chamber that meets your specific needs and allows you to conduct experiments and explore new possibilities. This endeavor provides not only a practical tool but also a valuable learning experience in the principles of physics, engineering, and materials science. Always remember that vacuum technology, while accessible, demands respect for safety and a commitment to understanding the underlying principles.
What materials are typically used for building a simple vacuum chamber, and why are they chosen?
Common materials include stainless steel, acrylic (Plexiglas), and glass. Stainless steel is often preferred for its strength, resistance to corrosion, and ability to maintain a good seal. It’s also relatively non-porous, minimizing outgassing, which is the release of trapped gases that can degrade the vacuum level.
Acrylic and glass offer excellent visibility, allowing you to observe the experiment inside the chamber. Acrylic is lighter and less brittle than glass, making it easier to work with, but it’s more susceptible to scratches and may have higher outgassing rates. Glass, particularly tempered glass, is stronger than acrylic and has lower outgassing, but it can be more difficult and costly to fabricate.
What type of vacuum pump is best suited for a DIY vacuum chamber, and what specifications should I look for?
For a simple DIY vacuum chamber, a two-stage rotary vane vacuum pump is generally recommended. These pumps are relatively affordable, readily available, and capable of achieving a decent vacuum level (typically in the range of 10^-2 to 10^-3 Torr), sufficient for many basic experiments. Consider oil-free scroll pumps as an alternative, although they often have a higher initial cost, they eliminate the risk of oil backstreaming into the chamber.
Key specifications to consider include the pumping speed (measured in liters per minute or cubic feet per minute), which determines how quickly the chamber can be evacuated, and the ultimate pressure (measured in Torr, mTorr, or Pascal), which represents the lowest pressure the pump can achieve. Ensure the pump’s pumping speed is adequate for the chamber volume and that the ultimate pressure is low enough for your intended application.
How do I ensure a proper seal between the chamber and the lid in my DIY vacuum chamber?
A proper seal is crucial for achieving a good vacuum. The most common method is to use an O-ring made of a suitable material like Viton or Buna-N rubber. These materials are chosen for their flexibility, resistance to vacuum conditions, and low outgassing rates. The O-ring should be properly sized to fit snugly within a groove or recess on either the chamber or the lid.
Ensure the surfaces that come into contact with the O-ring are clean, smooth, and free of any scratches or imperfections. Applying a thin layer of vacuum grease (specifically designed for vacuum applications) to the O-ring can further improve the seal and prevent leaks. Regularly inspect and replace the O-ring as needed, as it can degrade over time.
What are the potential safety hazards associated with operating a vacuum chamber, and how can I mitigate them?
Implosion is a significant risk, especially if the chamber is made of glass or acrylic. If the chamber walls are not strong enough to withstand the pressure difference, they can shatter violently inward. Always use appropriate safety glasses and consider enclosing the chamber in a protective cage or shield, particularly during initial testing.
Another hazard is the potential for outgassing of harmful substances. Materials within the chamber can release volatile compounds under vacuum, which can be toxic or flammable. Ensure that any materials placed inside the chamber are compatible with vacuum conditions and that adequate ventilation is provided in the surrounding area. Also, be cautious of high voltages or hot components within the chamber, following proper electrical safety protocols.
How can I monitor the vacuum level inside my DIY chamber?
A vacuum gauge, also known as a pressure sensor, is essential for monitoring the vacuum level. Several types of gauges are available, each with different ranges and accuracy levels. For a simple DIY chamber, a Pirani gauge is a common and relatively inexpensive option. These gauges measure the thermal conductivity of the gas inside the chamber, which changes with pressure.
Connect the gauge to a port on the chamber using vacuum fittings. Ensure the fittings are properly sealed to prevent leaks. Regularly calibrate the gauge to ensure accurate readings. Display the gauge’s output on a digital display or a multimeter. This allows you to track the pressure as the chamber is evacuated and monitor for any leaks or changes in the vacuum level.
How do I troubleshoot common problems, such as leaks, in my vacuum chamber?
Leaks are a frequent issue with vacuum chambers. One common method for detecting leaks is using a “sniffer” – a handheld device that detects specific gases, such as helium. Introduce a small amount of helium around potential leak points, such as seals, fittings, and welds. If the sniffer detects helium, it indicates a leak in that area.
Another method involves using a soapy water solution. Apply the solution to potential leak points. If bubbles form, it indicates a leak. Carefully tighten fittings and inspect seals for damage. If a seal is damaged, replace it. For persistent leaks, consider using a vacuum sealant, which is a special compound designed to fill small gaps and create a better seal. After addressing any suspected leaks, re-evacuate the chamber and monitor the pressure gauge to ensure the leak has been resolved.
Can I perform experiments involving high temperatures or strong magnetic fields inside my DIY vacuum chamber?
While possible, experiments involving high temperatures or strong magnetic fields require careful planning and material selection. High temperatures can cause materials to outgas more readily, degrading the vacuum level. Ensure that any components used for heating are compatible with vacuum conditions and are properly insulated to prevent overheating the chamber walls.
Strong magnetic fields can interfere with electronic components, including vacuum gauges and sensors. Shielding sensitive components may be necessary. Also, consider the interaction of the magnetic field with the chamber material, as some materials can become magnetized, which can affect the experiment. Consult relevant resources on vacuum technology and materials science for specific guidelines on safely conducting such experiments.
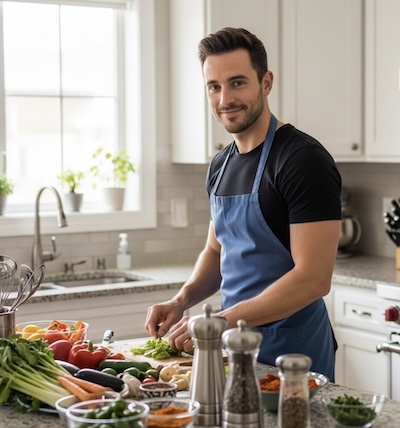
Alden Pierce is a passionate home cook and the creator of Cooking Again. He loves sharing easy recipes, practical cooking tips, and honest kitchen gear reviews to help others enjoy cooking with confidence and creativity. When he’s not in the kitchen, Alden enjoys exploring new cuisines and finding inspiration in everyday meals.