Edge grain wood, a common choice for various woodworking projects, presents a unique aesthetic and structural profile. Understanding its characteristics, advantages, and disadvantages is crucial for any woodworker aiming to make informed decisions about material selection. This article delves into the nuances of edge grain, exploring its appeal and potential drawbacks in detail.
Understanding Edge Grain
Edge grain refers to the orientation of wood where the annual growth rings are visible as relatively straight, vertical lines along the surface. This is achieved by cutting the lumber perpendicular to the growth rings, resulting in a surface primarily displaying the edges of those rings. This is in contrast to face grain (also known as flat grain), which showcases the broader, flatter surfaces of the growth rings, often resulting in cathedral-like patterns. End grain, on the other hand, displays the circular pattern of the tree’s growth rings when viewed at the cut end of the log. The way lumber is cut determines whether you get edge grain, face grain, or quarter sawn. Edge grain is usually obtained by cutting the log into planks that are parallel to the center.
Edge grain lumber is often desired for its strength and stability, but it’s important to consider all aspects before making a decision for your project. Its appearance, durability, and workability all play a role in determining its suitability.
The Advantages of Edge Grain
Edge grain boasts several advantages that make it a preferred choice for certain applications. These benefits range from enhanced structural integrity to a more subtle and consistent appearance.
Enhanced Stability and Durability
One of the most significant benefits of edge grain is its increased stability compared to face grain. Because the growth rings are oriented vertically, edge grain lumber is less prone to warping, cupping, and twisting as moisture content changes. This makes it an excellent choice for projects that will be exposed to varying humidity levels, such as tabletops, countertops, and flooring. The resistance to movement also translates to increased durability. The tight, vertical grain structure is less likely to splinter or dent under impact, making it suitable for high-traffic areas or surfaces subject to wear and tear.
Aesthetically Pleasing Uniformity
Edge grain offers a more uniform and consistent appearance compared to face grain. The straight, parallel lines of the growth rings create a clean, understated look that is often preferred in contemporary or minimalist designs. The lack of prominent grain patterns allows the natural color and texture of the wood to shine through, providing a subtle elegance that complements various styles. The uniformity of the grain also means that it ages gracefully and any wear is less likely to stand out against distinct patterns.
Improved Resistance to Wear and Tear
The close grain pattern of edge grain wood provides a harder and more durable surface. This is especially important for surfaces that experience frequent use, such as cutting boards or workbenches. The tight grain resists scratching and denting, maintaining its appearance over time. Edge grain’s resistance to wear also makes it a good choice for wood flooring in high-traffic areas of the home.
Better Glue Joint Strength
When joining wood pieces together, edge grain orientation offers superior glue joint strength compared to face grain. The parallel grain direction provides a larger surface area for the glue to adhere to, creating a stronger and more durable bond. This is particularly important in projects that require structural integrity, such as furniture construction. The vertical orientation of the grain also helps to distribute stress evenly across the joint, reducing the risk of failure.
The Drawbacks of Edge Grain
While edge grain offers several advantages, it also has some drawbacks that need to be considered. These can range from higher cost to potential challenges during the woodworking process.
Higher Cost and Limited Availability
Edge grain lumber can be more expensive than face grain due to the way it’s sawn from the log. The process yields less usable material compared to flat sawn lumber, increasing production costs. Additionally, edge grain lumber may be less readily available than face grain, especially in certain wood species or grades. This can make it more challenging to source the desired material for your project. Finding specific widths and lengths of edge grain lumber may also require more searching and potentially ordering from specialized suppliers.
Potential for Tear-Out During Machining
Working with edge grain can sometimes present challenges during machining, particularly when planing or routing against the grain. The tight grain structure can be prone to tear-out, resulting in a less-than-smooth surface. This requires careful technique, sharp tools, and sometimes the use of grain fillers to achieve a flawless finish. Understanding the grain direction and adjusting the feed rate of your tools can minimize the risk of tear-out.
Appearance Can Be Seen as “Plain”
While the uniform appearance of edge grain is often considered an advantage, some may find it visually less interesting than the more dynamic patterns of face grain. The lack of prominent grain features can make it appear “plain” or “boring” to some individuals. Depending on the aesthetic you’re aiming for, edge grain may not be the best choice if you desire a visually striking wood surface.
Difficulty in Matching Grain Patterns
Achieving seamless transitions and matching grain patterns across multiple pieces of edge grain lumber can be challenging. The subtle variations in grain direction and color can be more noticeable when trying to create a cohesive look. This requires careful selection and arrangement of boards to minimize any visual discrepancies. Unlike face grain where the cathedral pattern can aid in creating matching sections, edge grain requires careful planning and execution.
Applications of Edge Grain Wood
Edge grain wood is widely used in various woodworking projects due to its strength, stability, and aesthetic appeal. Here are some common applications:
Cutting Boards and Butcher Blocks
Edge grain is a preferred choice for cutting boards and butcher blocks because of its durability and resistance to knife marks. The vertical grain orientation allows the wood to “heal” itself as knife marks tend to close up, making it more hygienic and long-lasting. The hardness of the edge grain surface also prevents excessive dulling of knives.
Tabletops and Countertops
The stability and durability of edge grain make it an excellent option for tabletops and countertops. It resists warping and cupping, ensuring a flat and stable surface even in fluctuating humidity conditions. The uniform appearance also adds a touch of elegance to any room.
Flooring
Edge grain wood flooring is known for its durability and resistance to wear and tear. It’s a popular choice for high-traffic areas, providing a long-lasting and aesthetically pleasing surface. The dimensional stability of edge grain helps prevent gaps and warping, ensuring a beautiful floor for years to come.
Furniture Construction
Edge grain is often used in furniture construction, particularly for structural components like legs, rails, and stretchers. Its strength and stability provide a solid foundation for furniture pieces, ensuring long-term durability. The consistent appearance also contributes to a refined and elegant look.
Working with Edge Grain: Tips and Techniques
Working with edge grain requires some specific techniques to maximize its benefits and minimize potential challenges.
Sharp Tools are Essential
Using sharp tools is crucial when working with edge grain to prevent tear-out. Dull blades or chisels can cause the wood fibers to lift and splinter, resulting in a rough surface. Regularly sharpen your tools and consider using a lower cutting angle to minimize tear-out.
Control Feed Rate During Machining
The feed rate of your tools significantly impacts the quality of the cut when working with edge grain. Avoid forcing the tool through the wood, as this can increase the risk of tear-out. Instead, use a slow and steady feed rate, allowing the tool to cut cleanly.
Use a Backing Board When Routing
When routing edge grain, using a backing board can help prevent tear-out at the exit point of the cut. The backing board provides support to the wood fibers, preventing them from lifting and splintering. Clamp the backing board tightly against the workpiece to ensure a clean and smooth cut.
Consider Grain Fillers
If you experience tear-out despite taking precautions, consider using a grain filler to fill in any imperfections. Grain filler can help create a smooth and even surface, improving the overall finish of your project. Choose a grain filler that matches the color of your wood for a seamless look.
Proper Sanding Techniques
Proper sanding techniques are critical for achieving a smooth finish on edge grain. Start with a coarser grit sandpaper and gradually move to finer grits to remove any scratches or imperfections. Sand with the grain to avoid creating cross-grain scratches.
Choosing the Right Wood for Edge Grain
The species of wood significantly impacts the properties and appearance of edge grain. Some woods are better suited for edge grain applications than others.
Hardwoods vs. Softwoods
Hardwoods like maple, oak, and walnut are often preferred for edge grain projects due to their density and durability. They offer excellent resistance to wear and tear, making them ideal for cutting boards, countertops, and flooring. Softwoods, such as pine and fir, can also be used for edge grain projects, but they are generally less durable and more prone to denting.
Grain Density and Figure
The grain density and figure of the wood will influence the overall appearance of the edge grain surface. Woods with tighter grains tend to be more stable and less prone to tear-out. Woods with interesting figure, such as curly maple or birds eye maple, can add visual interest to edge grain projects, but they may also be more challenging to work with.
Color and Tone
Consider the color and tone of the wood when selecting lumber for your project. Different wood species offer a wide range of colors, from light and airy to rich and dark. Choose a wood that complements the overall aesthetic you’re aiming for.
Conclusion
Edge grain offers a unique combination of strength, stability, and aesthetic appeal, making it a valuable choice for a wide range of woodworking projects. While it has its drawbacks, such as higher cost and potential machining challenges, understanding its benefits and limitations allows woodworkers to make informed decisions and utilize it effectively. Whether you are crafting a durable cutting board, a stunning tabletop, or long-lasting flooring, edge grain can be a rewarding choice that enhances the beauty and longevity of your creations. By considering the specific requirements of your project and employing appropriate woodworking techniques, you can harness the full potential of edge grain and create pieces that will be admired for generations.
What exactly is edge grain in woodworking, and how does it differ from face grain and end grain?
Edge grain refers to the long, narrow surface of a board that runs parallel to the tree’s rings, often showcasing a tight, linear pattern. It is created when a board is sawn perpendicular to the growth rings. Visually, it sits between the wider, more prominent figure of the face grain and the dense, growth-ring-concentrated end grain.
Face grain, in contrast, is the wide, flat surface of a board displaying the broader patterns of the wood. End grain is the cross-section of the tree, exposed at the end of a board, revealing the tree’s age and growth characteristics. Understanding these distinctions is crucial for selecting the appropriate wood orientation for strength, stability, and aesthetic considerations in a woodworking project.
What are the primary benefits of using edge grain in woodworking projects?
Edge grain is highly regarded for its exceptional stability and resistance to warping or cupping. This stability stems from the way the wood fibers are oriented, which minimizes movement caused by changes in humidity. Consequently, edge grain surfaces tend to remain flat and true over time, making them ideal for applications where dimensional accuracy is essential.
Furthermore, edge grain offers a relatively smooth and durable surface. It often provides a more consistent texture than face grain, making it well-suited for applications that require a smooth finish and resistance to wear and tear. It also often offers a more understated aesthetic than face grain, letting the form of a piece speak for itself.
Are there any specific woodworking projects where edge grain is particularly advantageous?
Edge grain is particularly well-suited for applications where stability and durability are paramount, such as countertops, tabletops, and shelving. The resistance to warping makes it ideal for large, flat surfaces that need to remain true over time, even under fluctuating humidity levels. Its strength also lends itself to heavy-use applications.
Cutting boards are another excellent application for edge grain. The orientation of the wood fibers helps to minimize knife marks and prevent the wood from splintering, leading to a more durable and sanitary cutting surface. The close grain also helps inhibit the growth of bacteria, making edge grain a favored choice for food preparation surfaces.
What are some of the drawbacks or limitations of using edge grain in woodworking?
One potential drawback of using edge grain is that it can be more challenging to work with compared to face grain. The tight grain structure can sometimes make it more difficult to achieve a perfectly smooth finish, particularly when using hand tools. Careful sanding and finishing techniques are often required to overcome this challenge.
Aesthetically, edge grain may be considered less visually striking than face grain, which often displays more prominent and varied figure. While the understated appearance of edge grain is desirable in some cases, it may not be the preferred choice for projects where showcasing the wood’s natural beauty is a primary goal. Additionally, depending on the wood species, obtaining wide edge-grain boards may be more costly or difficult due to lumber grading and availability.
How does the type of wood species affect the suitability of using edge grain?
The suitability of using edge grain varies depending on the wood species’ inherent properties. Denser hardwoods like maple, walnut, and cherry typically exhibit excellent stability and durability when used in edge grain applications. Softwoods, on the other hand, may be more prone to denting and scratching, even in edge grain orientation.
Grain patterns also influence the aesthetic appeal of edge grain. Woods with tight, uniform grain, such as hard maple, tend to create a clean, consistent look, while species with more pronounced grain variations, like oak, will exhibit a more textured appearance. The choice of wood species will, therefore, depend on the desired balance between performance and visual characteristics.
What techniques or considerations are important when joining edge grain boards together?
When joining edge grain boards together, careful attention must be paid to proper alignment and gluing techniques. Ensuring that the edges are perfectly straight and square is crucial for creating a seamless and strong joint. Using a jointer and planer is highly recommended to achieve perfectly mated surfaces.
Employing sufficient clamping pressure during glue-up is also essential to ensure a strong and lasting bond. The type of glue used can also affect the joint’s strength and longevity. A high-quality wood glue specifically formulated for edge-to-edge joints is recommended. Consider alternating the grain direction of adjacent boards to further minimize the potential for warping or cupping in the finished piece.
Does edge grain require a different approach to finishing compared to face grain?
Edge grain often requires a slightly different approach to finishing compared to face grain due to its tighter pore structure. Because edge grain is less porous than face grain, it may absorb less stain or finish during the initial application. Therefore, it’s often necessary to apply multiple thin coats of finish to achieve the desired level of color and protection.
Sanding is also crucial for achieving a smooth and even finish on edge grain. Starting with a coarser grit sandpaper and gradually progressing to finer grits will help to remove any imperfections and create a consistent surface. Applying a sanding sealer before staining or finishing can also help to even out the absorption rate and prevent blotching, ultimately enhancing the final appearance.
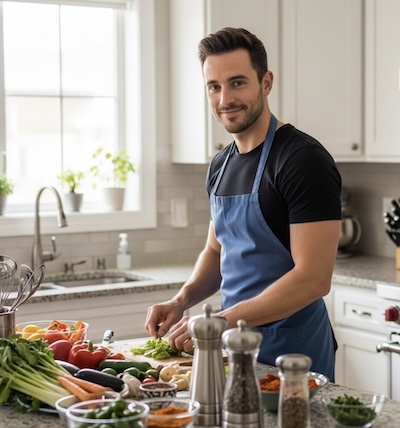
Alden Pierce is a passionate home cook and the creator of Cooking Again. He loves sharing easy recipes, practical cooking tips, and honest kitchen gear reviews to help others enjoy cooking with confidence and creativity. When he’s not in the kitchen, Alden enjoys exploring new cuisines and finding inspiration in everyday meals.