Temperature, a fundamental physical property, is a measure of the average kinetic energy of the particles within a substance. Accurately measuring temperature is crucial in a vast array of fields, from scientific research and industrial processes to medical diagnostics and everyday cooking. But with so many temperature measurement methods available, determining the “most accurate” can be complex and depends heavily on the specific application, temperature range, and required precision.
Understanding the Basics of Temperature Measurement
Before diving into specific methods, it’s important to understand some underlying principles. Temperature measurement relies on observing how a substance’s properties change with temperature. These properties can include volume (as in a liquid-in-glass thermometer), electrical resistance (as in a resistance thermometer), infrared radiation (as in an infrared thermometer), or even the color of emitted light (as in pyrometry).
Accuracy refers to how close a measurement is to the true value. Precision, on the other hand, refers to the repeatability of a measurement. A method can be precise without being accurate, and vice versa. The ideal temperature measurement method should possess both.
Other factors that influence the selection of a temperature measurement technique include: the temperature range to be measured, the required response time, the invasiveness of the method, and the cost. No single method reigns supreme in all situations.
Exploring Different Temperature Measurement Methods
Let’s examine some of the most common and accurate temperature measurement methods, highlighting their principles, advantages, and limitations.
Contact Thermometers: Direct Measurement of Substance Temperature
Contact thermometers achieve thermal equilibrium with the object being measured. This direct contact allows for a more precise measurement than non-contact methods, but requires physical interaction with the object, which can be a limitation in some scenarios.
Liquid-in-Glass Thermometers: The Familiar Standard
Liquid-in-glass thermometers are perhaps the most recognizable temperature measurement devices. They consist of a glass bulb filled with a liquid (typically mercury or alcohol) connected to a narrow glass tube. As the temperature rises, the liquid expands and rises in the tube, indicating the temperature on a calibrated scale.
Advantages: Relatively inexpensive, easy to use, and requires no external power source.
Disadvantages: Can be fragile, relatively slow response time, and potential for parallax error in reading the scale. Mercury thermometers are also increasingly restricted due to environmental concerns.
Resistance Temperature Detectors (RTDs): Precision through Resistance
RTDs are highly accurate temperature sensors that rely on the principle that the electrical resistance of a metal changes with temperature. They typically use a platinum wire or thin film, chosen for its stable and predictable resistance-temperature relationship.
Advantages: High accuracy and stability, wide temperature range (depending on the material), suitable for industrial applications requiring precise temperature control.
Disadvantages: Slower response time compared to thermocouples, more expensive than thermocouples, and require an external current source to measure the resistance.
Thermocouples: Versatility and Wide Range
Thermocouples consist of two dissimilar metal wires joined at one end (the “hot junction”). When the junction is heated or cooled, a voltage is produced (the Seebeck effect) that is proportional to the temperature difference between the hot junction and a reference junction (the “cold junction”).
Advantages: Wide temperature range, relatively inexpensive, fast response time, robust, and self-powered.
Disadvantages: Lower accuracy and stability compared to RTDs, requires cold junction compensation, and the voltage signal is small, requiring amplification. Different thermocouple types offer varying temperature ranges and sensitivities. Common types include Type K, Type J, Type T, and Type E.
Thermistors: High Sensitivity within a Limited Range
Thermistors are semiconductor devices whose electrical resistance changes significantly with temperature. They are highly sensitive and offer excellent accuracy within a limited temperature range.
Advantages: High sensitivity, small size, relatively inexpensive.
Disadvantages: Non-linear resistance-temperature relationship, limited temperature range, and susceptible to self-heating if excessive current is passed through them.
Non-Contact Thermometers: Measuring Temperature from a Distance
Non-contact thermometers measure temperature without physically touching the object. This is particularly useful for measuring the temperature of moving objects, hazardous materials, or objects at very high temperatures.
Infrared (IR) Thermometers: Detecting Thermal Radiation
IR thermometers detect the infrared radiation emitted by an object. The amount of radiation emitted is proportional to the object’s temperature. They often use a lens to focus the infrared energy onto a detector, which converts the radiation into an electrical signal that is displayed as a temperature reading.
Advantages: Fast response time, can measure temperature from a distance, suitable for moving objects or hazardous environments.
Disadvantages: Accuracy can be affected by the emissivity of the object (its ability to emit infrared radiation), susceptible to interference from ambient infrared radiation, and can be influenced by obstructions between the thermometer and the object. Emissivity correction is crucial for accurate readings.
Pyrometers: Measuring Incandescent Objects
Pyrometers are used to measure the temperature of very hot objects, such as molten metal or furnaces. They operate by analyzing the color or intensity of the light emitted by the object.
Advantages: Can measure very high temperatures, non-contact measurement.
Disadvantages: Requires the object to be incandescent, accuracy depends on the object’s emissivity, and can be complex and expensive.
Factors Affecting Accuracy and Choosing the Right Method
Selecting the most accurate temperature measurement method requires careful consideration of several factors:
- Temperature Range: Different thermometers have different temperature ranges. Choose a thermometer whose range encompasses the temperature you need to measure.
- Accuracy Requirements: Determine the level of accuracy required for your application. RTDs generally offer the highest accuracy, followed by thermocouples and then liquid-in-glass thermometers. IR thermometers are less accurate but offer the convenience of non-contact measurement.
- Response Time: Consider how quickly the temperature is changing. Thermocouples and IR thermometers have the fastest response times, while RTDs and liquid-in-glass thermometers are slower.
- Environment: The environment in which the measurement is taken can also affect accuracy. Factors such as humidity, electromagnetic interference, and corrosive substances can all impact the performance of different thermometers.
- Object Properties: The properties of the object being measured, such as its emissivity (for IR thermometers) and thermal conductivity, can also influence the accuracy of the measurement.
- Cost: The cost of the thermometer and any associated equipment should also be considered.
Calibration and Traceability
Regardless of the temperature measurement method used, regular calibration is essential to ensure accuracy. Calibration involves comparing the thermometer’s readings to a known standard and adjusting the thermometer accordingly.
Traceability refers to the ability to link a measurement back to a recognized standard, such as the International Temperature Scale of 1990 (ITS-90). Traceable calibration provides confidence in the accuracy and reliability of temperature measurements.
Laboratories that perform temperature calibrations often maintain accreditation from organizations like NIST (National Institute of Standards and Technology) or other national metrology institutes. This accreditation ensures that the laboratory’s calibration procedures meet rigorous standards and that the measurements are traceable to national or international standards.
Advances in Temperature Measurement Technology
Temperature measurement technology is constantly evolving. New sensor materials, advanced signal processing techniques, and improved calibration methods are leading to more accurate, reliable, and versatile temperature measurement solutions.
Fiber optic thermometers, for example, offer high accuracy and immunity to electromagnetic interference, making them suitable for demanding applications in medical and industrial settings.
Micro-sensors and wireless sensor networks are enabling temperature monitoring in remote locations and in applications where traditional wired sensors are impractical.
Conclusion: Defining the Most Accurate Method
So, what is the most accurate method to measure temperature? There is no single definitive answer. The most accurate method depends on the specific application, the temperature range of interest, the required accuracy, and other practical considerations.
For high-precision laboratory measurements, RTDs are often the preferred choice due to their excellent accuracy and stability. In industrial settings where robustness and a wide temperature range are important, thermocouples are frequently used. For non-contact measurements, IR thermometers provide a convenient option, although careful attention must be paid to emissivity and other factors that can affect accuracy.
Ultimately, selecting the right temperature measurement method requires a thorough understanding of the principles behind each method, their limitations, and the specific requirements of the application. Proper calibration and traceability are also essential to ensure the accuracy and reliability of temperature measurements.
What factors influence the accuracy of temperature measurement?
Several factors can significantly impact the accuracy of temperature measurements. These include the type of sensor used, the calibration of the instrument, environmental conditions, and the thermal contact between the sensor and the object being measured. Selecting the right sensor for the temperature range and application is crucial, as each sensor type has inherent limitations. Furthermore, proper calibration against a known standard is essential to ensure that the instrument provides readings within acceptable tolerance levels.
Environmental factors like ambient temperature, humidity, and electromagnetic interference can all influence the accuracy of temperature measurements. In addition, ensuring good thermal contact between the sensor and the object being measured is vital to minimize errors due to thermal resistance. This might involve using thermal paste, selecting appropriate mounting techniques, or considering the sensor’s response time to changes in temperature.
What are the primary differences between contact and non-contact temperature measurement methods?
Contact temperature measurement methods involve physically touching the object being measured with a sensor. These methods, such as using thermocouples, resistance temperature detectors (RTDs), or thermistors, rely on thermal equilibrium between the sensor and the object. The sensor’s temperature changes until it matches the object’s temperature, and this temperature is then measured.
Non-contact temperature measurement methods, like infrared thermometers or thermal cameras, measure the infrared radiation emitted by an object. These methods do not require physical contact and are suitable for measuring the temperature of moving objects, hazardous materials, or objects at high temperatures. However, the accuracy of non-contact methods can be affected by the object’s emissivity, ambient temperature, and distance from the sensor.
How does the choice of sensor type impact the accuracy of temperature measurement?
The choice of sensor type significantly impacts the accuracy of temperature measurements because different sensors have varying degrees of sensitivity, linearity, and response time. For example, thermocouples are robust and can measure a wide range of temperatures, but they tend to be less accurate than RTDs. RTDs offer high accuracy and stability but are more expensive and have a slower response time.
Thermistors are highly sensitive and suitable for precise temperature measurements within a narrow range, but their non-linear response requires more complex signal conditioning. Infrared thermometers are convenient for non-contact measurements, but their accuracy depends heavily on the emissivity of the target object and environmental conditions. Therefore, selecting the appropriate sensor based on the specific application requirements is crucial for achieving accurate temperature measurements.
What is the role of calibration in ensuring accurate temperature measurements?
Calibration plays a crucial role in ensuring accurate temperature measurements by establishing a relationship between the sensor’s output and the actual temperature. This process involves comparing the sensor’s readings against a known standard temperature source and adjusting the instrument to minimize deviations. Regular calibration is essential to compensate for sensor drift, aging, and environmental factors that can affect the accuracy of measurements over time.
Proper calibration ensures that the sensor’s output corresponds accurately to the true temperature of the object being measured. Without calibration, the sensor’s readings may deviate significantly from the actual temperature, leading to erroneous results and potentially impacting critical processes or decisions. Calibration is a fundamental aspect of metrology and is vital for maintaining the reliability and integrity of temperature measurements.
What are some common sources of error in temperature measurement, and how can they be minimized?
Common sources of error in temperature measurement include thermal resistance, sensor self-heating, environmental effects, and improper sensor placement. Thermal resistance between the sensor and the object being measured can lead to inaccurate readings. This can be minimized by using thermal paste, ensuring good contact, and selecting appropriate mounting techniques.
Sensor self-heating occurs when the sensor dissipates heat, affecting the temperature of the object being measured. This can be mitigated by using sensors with low power consumption and minimizing the measurement time. Environmental effects, such as ambient temperature fluctuations and electromagnetic interference, can also introduce errors. Shielding the sensor, compensating for ambient temperature, and using appropriate filtering techniques can help minimize these errors. Lastly, proper sensor placement is crucial to ensure that the sensor measures the temperature of the desired location and is not influenced by external heat sources or sinks.
How do environmental factors affect the accuracy of infrared temperature measurement?
Environmental factors significantly impact the accuracy of infrared (IR) temperature measurement because IR thermometers measure the thermal radiation emitted by an object, which can be affected by atmospheric conditions and the surrounding environment. Ambient temperature, humidity, and the presence of particulate matter can all influence the amount of infrared radiation reaching the sensor.
For example, high humidity can absorb some of the infrared radiation, leading to lower temperature readings. Similarly, dust or smoke in the air can scatter or absorb infrared radiation, affecting the accuracy of the measurement. Therefore, it is essential to consider these environmental factors and, if necessary, apply corrections or adjustments to the IR thermometer’s readings to obtain more accurate results. Furthermore, the emissivity of the target object is also a critical factor, as it determines the amount of infrared radiation emitted at a given temperature.
What are the advantages and disadvantages of using resistance temperature detectors (RTDs)?
Resistance Temperature Detectors (RTDs) offer several advantages, including high accuracy, stability, and linearity over a wide temperature range. They are less susceptible to drift compared to thermocouples and provide more repeatable measurements. RTDs are also relatively immune to electromagnetic interference, making them suitable for industrial environments.
However, RTDs also have some disadvantages. They are generally more expensive than thermocouples and have a slower response time, which can be a limitation in applications requiring rapid temperature changes. Additionally, RTDs require an external excitation current, which can cause self-heating and introduce errors if not properly managed. They are also typically more fragile than thermocouples and may be less suitable for harsh environments.
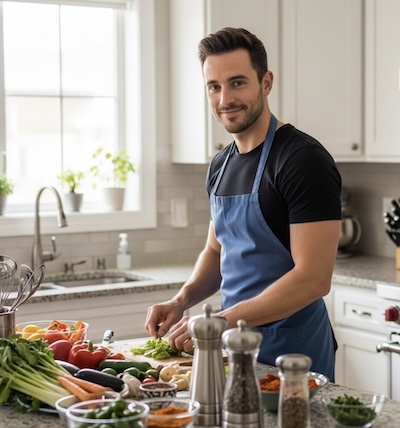
Alden Pierce is a passionate home cook and the creator of Cooking Again. He loves sharing easy recipes, practical cooking tips, and honest kitchen gear reviews to help others enjoy cooking with confidence and creativity. When he’s not in the kitchen, Alden enjoys exploring new cuisines and finding inspiration in everyday meals.