Screen printing is a versatile and rewarding printing technique, allowing you to create stunning designs on a variety of surfaces. A crucial step in the screen printing process is exposing your emulsion-coated screen to light, creating the stencil that will define your printed image. But how long do you expose emulsion? The answer, unfortunately, isn’t a simple number. It’s a complex interplay of various factors, and understanding these elements is key to achieving crisp, clean prints. This comprehensive guide will delve into the variables that influence exposure time, providing you with the knowledge to optimize your screen printing process.
Understanding Emulsion and Its Role
Emulsion is a light-sensitive liquid that, when applied to a screen printing mesh, forms a stencil after being exposed to ultraviolet (UV) light. It hardens in the areas exposed to light, while the unexposed areas remain soft and can be washed away, leaving behind the desired image. The type of emulsion you choose plays a significant role in determining the appropriate exposure time.
Different Types of Emulsion
Different emulsions react differently to light sources. Some emulsions are faster-acting, requiring shorter exposure times, while others need more extended exposure. Popular types include:
Diazo Emulsion: Known for its durability and forgiving nature. It typically requires longer exposure times than other types. It is a good all-around choice for beginners.
Photopolymer Emulsion: Offers faster exposure times and excellent resolution. It’s a popular choice for intricate designs and halftone printing. This emulsion is often pre-sensitized, meaning you don’t have to mix it with a sensitizer before use.
Dual-Cure Emulsion: A hybrid combining the benefits of both diazo and photopolymer emulsions. It provides a balance of durability and speed.
Understanding the specific characteristics of your chosen emulsion is paramount. Refer to the manufacturer’s instructions for recommended exposure times as a starting point. Don’t just guess – knowledge is power!
The Exposure Unit: Your Light Source
The type of exposure unit you use is another major factor influencing exposure time. Different light sources emit varying intensities and wavelengths of UV light, impacting how quickly the emulsion hardens.
Types of Exposure Units and Their Impact
Here are the most common types of exposure units used in screen printing:
UV Fluorescent Tubes: A common and affordable option. However, they tend to have lower UV output compared to other options, resulting in longer exposure times. The age of the bulbs can also affect the UV output, so replace them regularly.
Metal Halide Lamps: These lamps emit a powerful, broad spectrum of UV light, allowing for much faster exposure times. They are often used in professional screen printing setups. These lamps generate a significant amount of heat, requiring proper ventilation.
LED Exposure Units: LED units are becoming increasingly popular due to their energy efficiency, long lifespan, and consistent UV output. They offer precise control over exposure times and are a good middle ground in terms of cost and performance.
Sunlight: While possible, using sunlight is highly unreliable due to its inconsistent intensity and unpredictable nature. This method is not recommended for achieving consistent and professional results. The level of UV light is also dangerous and can cause skin damage.
The intensity and spectrum of light emitted by your exposure unit directly affect the time it takes to properly expose the emulsion. A powerful light source will generally require shorter exposure times.
Mesh Count and Its Influence
The mesh count of your screen refers to the number of threads per inch or centimeter. Higher mesh counts have finer openings, which can affect how much light reaches the emulsion during exposure.
How Mesh Count Affects Exposure Time
Higher Mesh Counts (e.g., 305): These screens have finer openings, which can slightly reduce the amount of light that reaches the emulsion. This might necessitate a slightly longer exposure time compared to lower mesh counts.
Lower Mesh Counts (e.g., 110): These screens have larger openings, allowing more light to pass through. This might allow for a shorter exposure time.
The difference in exposure time between different mesh counts is often minimal, but it’s something to consider, especially when working with very fine details or halftones.
Stencil Thickness: Coating Your Screen
The thickness of the emulsion layer on your screen also plays a crucial role. A thicker layer of emulsion requires more time to harden completely.
Factors Affecting Stencil Thickness
Number of Coats: More coats of emulsion result in a thicker stencil. It is very common to apply two coats to each side.
Emulsion Viscosity: Thicker emulsions create thicker stencils.
Scoop Coater Technique: The angle and pressure applied while using a scoop coater affect the thickness of the emulsion layer. Consistent coating techniques are vital.
Thicker stencils are often desirable for printing on thicker substrates, such as fabrics, as they provide more ink deposit. However, they require longer exposure times. It is important to find a balance.
Artwork and Image Density
The opacity of your artwork and the density of the image on the transparency film also influence the amount of UV light that reaches the emulsion.
Impact of Artwork Opacity
Opaque Artwork: Blocks UV light effectively, ensuring the unexposed areas remain soft and washable.
Translucent Artwork: Allows some UV light to pass through, potentially leading to partially hardened emulsion in the unexposed areas, resulting in a poor stencil.
Ensure your artwork is printed with a high-density black ink on a transparent film designed for screen printing. Use a densitometer to measure the opacity of your film if you are uncertain.
The Step Test: Your Ultimate Exposure Guide
Given the multitude of factors that affect exposure time, the best way to determine the optimal exposure time for your specific setup is to perform a step test.
Conducting a Step Test
A step test involves exposing the same screen to different exposure times in increments. This allows you to visually assess which exposure time produces the best results.
- Prepare your screen as you normally would with emulsion and let it dry completely.
- Create a step test transparency. You can find templates online or create your own using image editing software. The template should have different numbered steps and contain various design elements like fine lines, text, and solid blocks.
- Place the transparency on the screen and cover a portion of the screen with an opaque material.
- Expose the uncovered portion of the screen for a specific time (e.g., 2 minutes).
- Move the opaque material to reveal another section of the screen.
- Expose the newly revealed section for a shorter time (e.g., 30 seconds less than the previous).
- Repeat steps 5 and 6, decreasing the exposure time for each step.
- Wash out the screen.
Evaluating the Results
After washing out the screen, examine the different steps. The ideal exposure time is the one that:
- Holds fine lines and details without washing out.
- Has solid blocks that are completely hardened.
- Shows no signs of a sticky or slimy residue.
- Reproduces the image accurately.
The step test provides valuable insights into how your emulsion reacts to your specific light source and setup. Document the optimal exposure time for future reference.
Environmental Factors: Temperature and Humidity
The temperature and humidity of your working environment can also affect emulsion drying and exposure.
Optimal Environmental Conditions
Temperature: Emulsion typically dries and exposes best in moderate temperatures (around 70-75°F or 21-24°C).
Humidity: High humidity can slow down the drying process and affect the emulsion’s sensitivity to light. Keep humidity levels below 50% if possible.
Use a dehumidifier or air conditioner to control humidity levels, especially in damp environments.
Troubleshooting Common Exposure Problems
Even with careful planning, you might encounter problems during exposure. Here are some common issues and how to address them:
Under-Exposure
Symptoms: The emulsion washes out completely, leaving no stencil, or the stencil is weak and easily damaged.
Causes: Insufficient exposure time, weak light source, translucent artwork, or expired emulsion.
Solutions: Increase exposure time, replace light source, improve artwork opacity, or use fresh emulsion.
Over-Exposure
Symptoms: The emulsion is difficult to wash out, even in the unexposed areas, or the stencil is hard and brittle.
Causes: Excessive exposure time, strong light source, or overly sensitive emulsion.
Solutions: Decrease exposure time, move the light source further away, or use a less sensitive emulsion.
Pinholes
Symptoms: Small holes appear in the stencil, allowing ink to pass through in unwanted areas.
Causes: Dust or debris on the screen, air bubbles in the emulsion, or insufficient exposure.
Solutions: Clean the screen thoroughly before coating, degas the emulsion to remove air bubbles, or increase exposure time slightly.
Final Thoughts: Practice and Consistency
Determining the optimal exposure time for your screen printing setup requires experimentation and careful observation. The step test is your most valuable tool for fine-tuning the process. Remember to document your findings and maintain consistent procedures to ensure reliable and high-quality results.
By understanding the factors that influence exposure time and by diligently performing step tests, you can master the art of screen printing and consistently produce professional-looking prints. Embrace the learning curve, experiment with different variables, and never stop refining your process. Happy printing!
How does the type of emulsion affect exposure time?
The type of emulsion used significantly impacts the ideal exposure time. Different emulsions have varying levels of photosensitivity. For instance, diazo emulsions generally require longer exposure times compared to dual-cure or photopolymer emulsions due to their lower sensitivity to UV light. Always consult the emulsion manufacturer’s datasheet for specific recommendations regarding exposure times based on your light source and other influencing factors.
Failure to consider the emulsion type can result in either underexposure or overexposure. Underexposure occurs when the emulsion isn’t sufficiently hardened, leading to stencil breakdown during printing. Overexposure, on the other hand, hardens the emulsion excessively, making it difficult to wash out the unexposed areas and resulting in a stencil that doesn’t allow ink to pass through properly.
What role does the light source play in emulsion exposure?
The light source is a crucial factor in determining the appropriate emulsion exposure time. Different light sources emit varying intensities and wavelengths of UV light, which directly affect the emulsion’s hardening process. LED exposure units, for example, are highly efficient and often require significantly shorter exposure times compared to fluorescent or metal halide lamps.
The distance between the light source and the screen also impacts exposure time. A closer light source delivers higher intensity UV light, thereby reducing the necessary exposure duration. It’s imperative to calibrate your exposure unit and establish a baseline exposure time using a step test to account for the specific characteristics of your light source and its distance from the screen.
Why is a step test essential for determining exposure time?
A step test, also known as an exposure calculator test, is an essential process for determining the optimal exposure time for your specific setup. It involves exposing a small section of the coated screen in incremental time steps, usually masked by a specialized tool or opaque material. This allows you to observe the emulsion’s reaction to varying exposure durations and identify the point at which it is properly hardened.
By examining the step test results, you can determine the shortest exposure time that produces a hard, durable stencil with sharp edges and fine detail retention. This eliminates guesswork and minimizes the risk of stencil failure during printing. A properly conducted step test is the most accurate method to calibrate your exposure unit and optimize your printing results.
How does mesh count influence exposure time?
Mesh count, or the number of threads per inch or centimeter, affects the amount of emulsion needed and consequently, the required exposure time. Lower mesh counts, such as 110 or 156, typically require thicker emulsion coatings, especially when printing on coarser materials. This increased emulsion thickness necessitates longer exposure times to ensure complete and uniform hardening.
Higher mesh counts, like 305 or 355, often require thinner emulsion layers due to their finer weave. These thinner layers require less exposure time. Neglecting to consider the mesh count can lead to stencils that are either underexposed and fragile or overexposed and difficult to wash out.
What environmental factors can affect emulsion exposure?
Environmental factors such as humidity and temperature can significantly influence emulsion exposure. High humidity can slow down the emulsion drying process and affect its sensitivity to UV light. Emulsion can absorb moisture from the air, potentially weakening its ability to harden properly during exposure.
Temperature fluctuations can also impact the emulsion’s characteristics. Extremely cold temperatures can make the emulsion more viscous, while excessively warm temperatures can cause it to dry too quickly or unevenly. Ideally, emulsion should be stored and used in a temperature-controlled environment with moderate humidity to ensure consistent and predictable results.
What are the signs of an underexposed stencil and how do you fix it?
An underexposed stencil often exhibits a soft or tacky surface. During washout, the image areas may wash away prematurely or lack fine detail. The emulsion may also feel slippery or dissolve easily when touched. In extreme cases, the entire stencil may dissolve during the washout process.
To fix underexposure, increase the exposure time in small increments, such as 10-15%, and repeat the step test. Ensure your light source is functioning correctly and that the distance between the light and the screen is appropriate. Consider adjusting the coating thickness to ensure sufficient emulsion coverage.
What are the signs of an overexposed stencil and how do you fix it?
An overexposed stencil is characterized by a very hard, glossy surface that is difficult to wash out. Fine details may be completely blocked, and the unexposed areas may be stubbornly resistant to removal. You might find it nearly impossible to achieve a clean, open image. The emulsion around the edges of the image might also have a jagged or chipped appearance.
To fix overexposure, decrease the exposure time in small increments, such as 10-15%, and repeat the step test. Check your light source’s intensity to ensure it hasn’t increased unexpectedly. Ensure the emulsion coating is consistent and not too thin, as a thin layer can overexpose more easily.
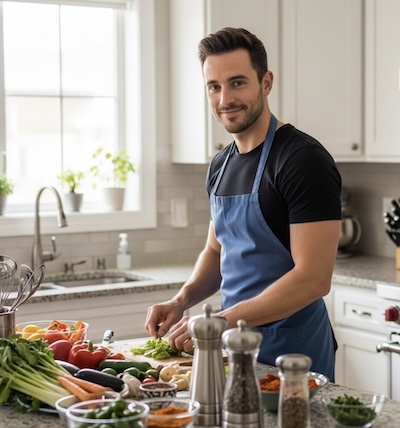
Alden Pierce is a passionate home cook and the creator of Cooking Again. He loves sharing easy recipes, practical cooking tips, and honest kitchen gear reviews to help others enjoy cooking with confidence and creativity. When he’s not in the kitchen, Alden enjoys exploring new cuisines and finding inspiration in everyday meals.